Concrete Block Pre-curing, Cutting Section
In the pre-curing section, the concrete block is placed between the mold and side plate, and conveyed to the pre-curing room for pre-curing through the use of a friction drive wheel. The pre-curing time is about 2-4 hours depending on the raw materials and finished products.
-
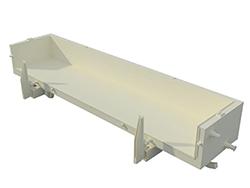
- Block Mould
The block mold is a vessel for pouring concrete blocks. The mold consists of the mold frame, side plate (base plate), and clamping arm.
The mold frame is formed by structural steel and steel plate, leading to a durable structure and high rotational sensitivity. Both ends are equipped with an overturn shaft and sealing strip to prevent leakage of slurry.
-
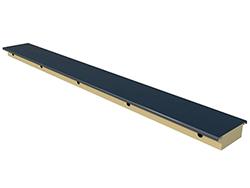
- AAC Mould Side Plate
Side plates are primarily used with a mold for loading slurry in AAC block production lines. After the demolding process using a lifting appliance, the side plate loaded with AAC blocks will be separated and conveyed into the concrete curing autoclave until packaging section.
-
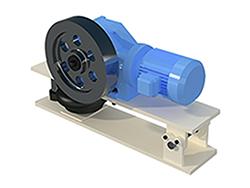
- Friction Drive Wheel
A friction drive wheel is used for mold sliding in the pre-curing room. With a compact structure, stable operation, and easy installation and repair, the friction drive wheel is suitable for automatic conveying of molds.
The concrete block and mold will be automatically pulled out after pre-curing, and conveyed to the overturn table and automatically positioned. The overturn table will automatically move above the mold, and lift it, then tilt and move the mold to above the cutting trolley to place the concrete block in the cutting trolley. The tilting table will then unlock the locking device, and finish demolding.
-
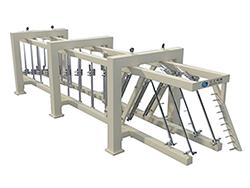
- AAC Block Cutter
When poured, AAC blocks are conveyed to the transfer cart with a 90 degree turning in the air, thus, demolding them. The first transfer cart will then convey them to the longitudinal cutter for longitudinal cutting. When the second transfer cart passes through the horizontal cutter, a hydraulic jack will place the concrete blocks into the second transfer cart for horizontal cutting.
When the cut concrete block leaves the cutting trolley, some waste materials will be produced on the bottom of concrete block due to bonding. The concrete block bottom cutter is designed in order to reduce the hard waste.
-
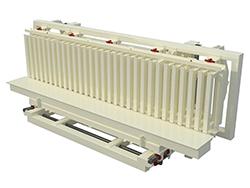
- Overturn Table (Tilting Table)
In an AAC production line, the cut concrete blocks will be turned 90 degrees by the overturn table, and waste material will be removed from the top of the block to the bottom using a scraper. Waste materials will be produced on the bottom of the concrete blocks after cutting. After turned 90° by the overturn table, the waste materials will drop automatically through gravitational force.
After demolding, the empty mold and empty side plates are combined together again and automatically enter the turning lane for the next pouring process.
-
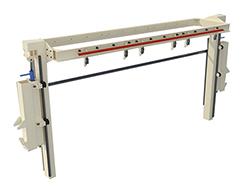
- Concrete Block Bottom Cutter
When the cut concrete block leaves the cutting trolley, waste materials will be produced on the bottom of concrete block due to bonding. The concrete block bottom cutter is designed to reduce the hard waste. Due to the risk of damaging the concrete blocks, the entire concrete block bottom cutter is equipped with a hydraulic buffer system and controlled by proportional valve.
Basic Parameters for Pre-curing
- Pre-Curing Time for Fly Ash: 150-180min
- Pre-Curing Time for Sand AAC Block: 180-210min
- Pre-Curing Time for AAC Block: 45℃-55℃
- Strength of Concrete Block after Pre-Curing: 0.15MPa-0.18MPa